The accuracy of on-board weighing systems is directly critical to the efficiency and compliance of transportation supervision and engineering measurement. SeeZol has continuously carried out systematic optimization from four core dimensions: sensor selection, algorithm optimization, error compensation, and anti-interference design, significantly improving its measurement accuracy.
Sensor Selection: The Cornerstone of Precise Measurement
SeeZol selects digital weighing sensors with built-in temperature compensation and A/D conversion chips, achieving an accuracy of up to 0.05%FS to effectively reduce signal loss. The measuring range is configured at 1.2-1.3 times the maximum vehicle load to ensure durability. Meanwhile, the sensors have an IP67 protection rating and a wide temperature working capability of -40°C to 85°C. During installation, high-strength bolts and rubber shock-absorbing pads are used to significantly reduce vibration interference.
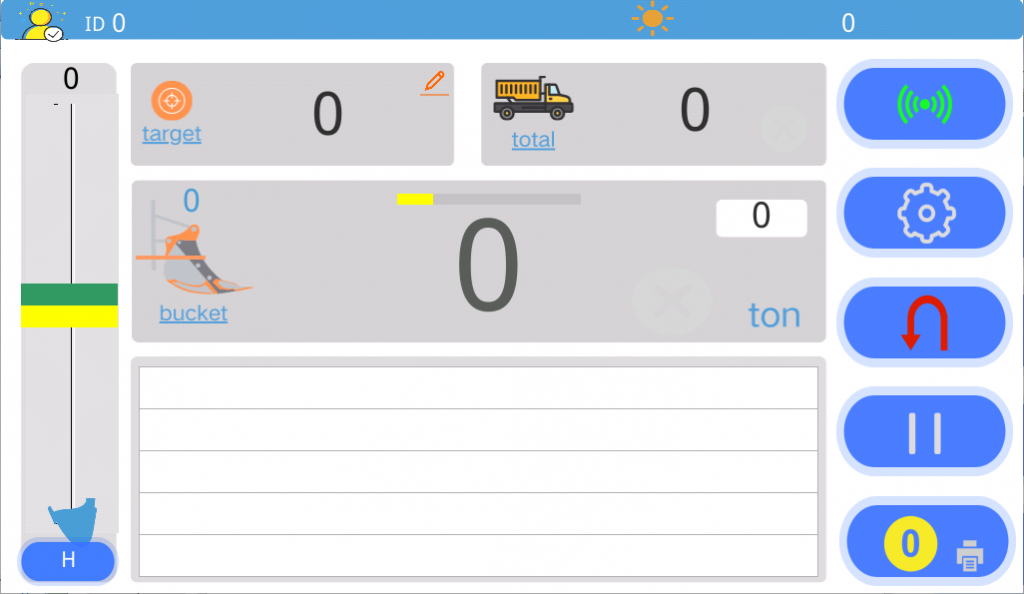
Algorithm Optimization: The Core Technology for Dynamic Measurement
SeeZol abandons traditional single algorithms and adopts a combination of multiple algorithms, integrating weighing signals with IMU acceleration data to real-time filter out vibration noise caused by vehicle bumps and sudden braking. Inertial force compensation is calculated based on acceleration and inclination data to correct dynamic load deviations. For non-linear errors, a precise correction model is established through polynomial fitting using three-point calibration (no-load, half-load, and full-load). When multiple sensors are networked, the angular difference matrix calculation technology is used to calibrate measurement deviations between sensors.
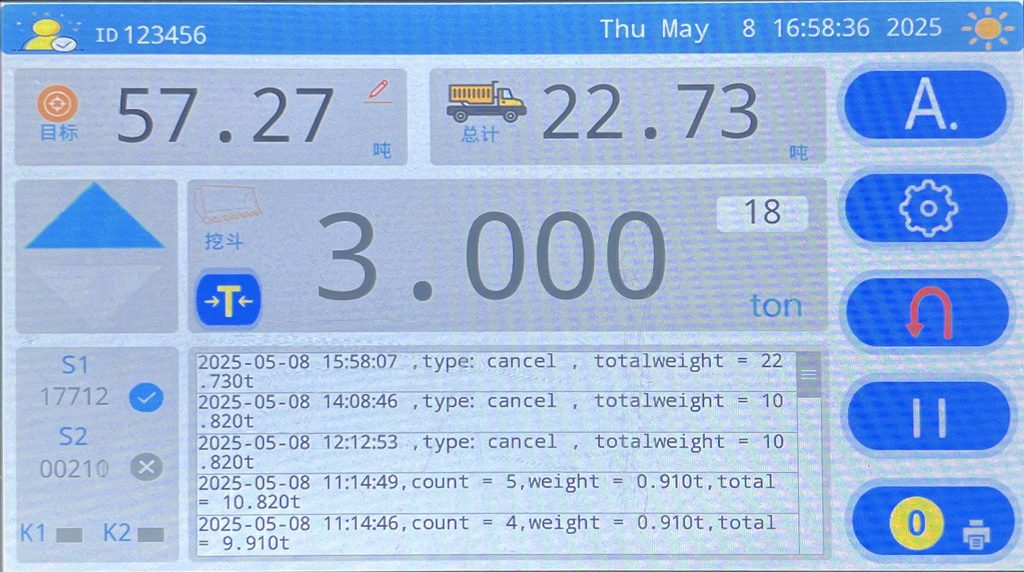
Error Compensation: Eliminating Systematic Deviations
In terms of temperature compensation, SeeZol uses hardware with series NTC thermistors to automatically adjust the bridge arm resistance, and software with a temperature-error mapping table at 5°C intervals to achieve real-time correction. The zero drift problem is solved by automatic zeroing when the vehicle is stationary and low-pass filtering. For off-center loading, the least squares method is used to fit the load distribution, ensuring that the difference between sensors is ≤1%FS.
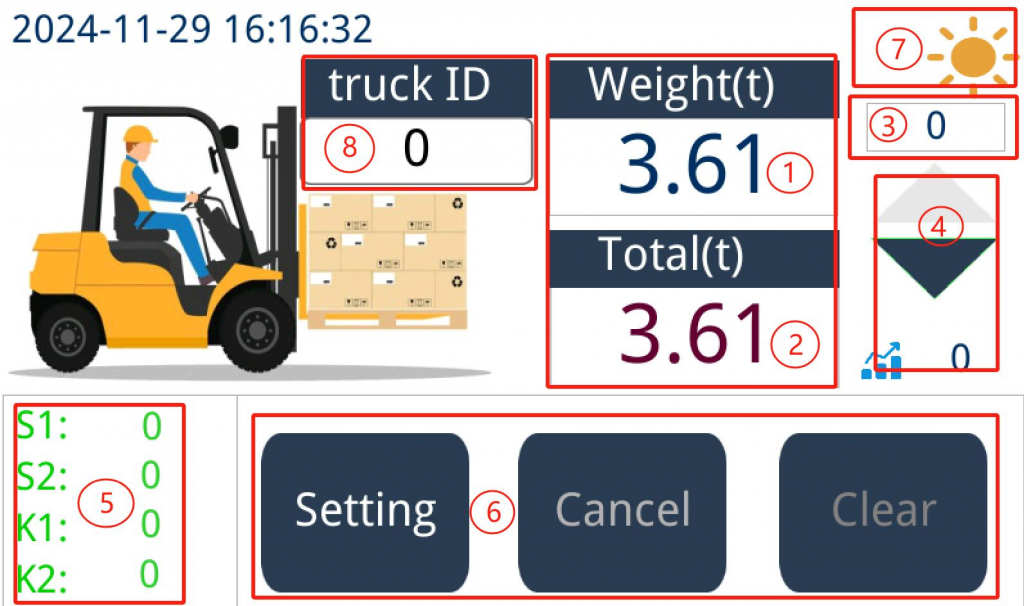
Anti-Interference Design: Ensuring Data Reliability
In terms of electromagnetic protection, SeeZol uses twisted-pair shielded cables with single-ended grounding, combined with isolated power modules and π-type filter circuits to effectively suppress electromagnetic interference from the engine. Mechanically, metal bellows shock absorbers are installed, and bolts are secured with thread-locking adhesive to prevent loosening. The communication uses CAN bus with CRC-16 verification, combined with the IQR algorithm to eliminate outliers, ensuring zero-error data transmission.
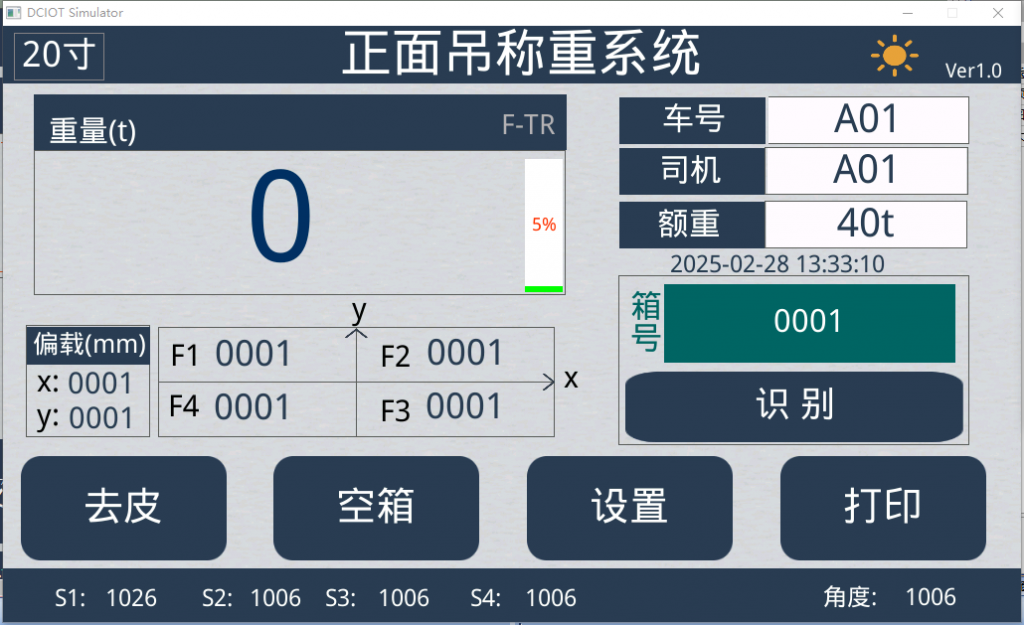
Through the above optimizations, the dynamic measurement error of SeeZol’s on-board weighing system can be reduced from the traditional 5% to within 1.5%, meeting the high-precision requirements of road transportation, engineering operations, and other fields, and providing a reliable support for intelligent transportation and industrial automation.It is widely used in various construction machinery requiring precise weighing, such as excavator scales, wheel loader scales, and forklift scales.