The load moment indicator system of excavator cranes is a crucial device for ensuring the safe operation of the equipment. To ensure its continuous, stable and accurate operation and effectively prevent safety accidents caused by moment overload, this daily maintenance plan is hereby formulated. This plan is applicable to all excavator cranes equipped with a safe load indicator system, covering daily inspections, regular maintenance, special maintenance and other contents, aiming to standardize the maintenance process, extend the service life of the system and improve the safety of equipment operation.
Daily Maintenance
Appearance Inspection: Conduct a comprehensive inspection of the appearance of sensors, circuits, controllers and actuators before operation, and check for any physical damage or loose connections. Pay special attention to the installation position of the sensors to ensure there is no deviation. Manually test the alarm device to ensure that the audible and visual alarms are working properly.
Function Pre-assessment: Turn on the power of the system and closely observe the self-check process, paying attention to any error codes. After starting the crane, run it under no-load for a while to verify the real-time response of the system to the movements of the jib and ensure the accuracy of the data display.
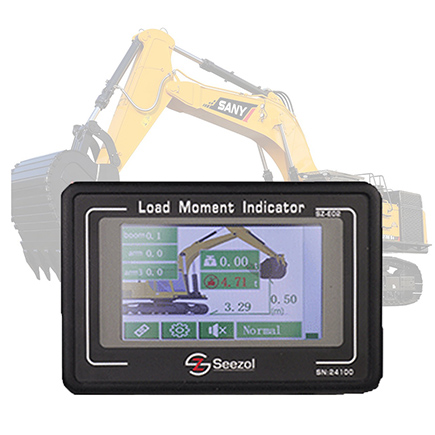
Weekly Maintenance
Sensor Maintenance: Clean all kinds of sensors to ensure that the sensing parts are not blocked. Check the connecting circuits to eliminate potential risks of looseness and oxidation. Use professional measuring tools to calibrate angle and length sensors, and compare the actual value and the displayed value of the pressure to judge the accuracy of the pressure sensor.
Circuit Maintenance: Check for wear, aging and breakage of the circuits, and repair or replace the damaged circuits in a timely manner. Clean the dust and oil stains on the circuits, and reinforce the fixing devices to ensure the stability of the circuits.
Controller Maintenance: Clean the outer shell and heat dissipation components of the controller, test the grounding resistance to ensure that the grounding meets the electrical safety standards.
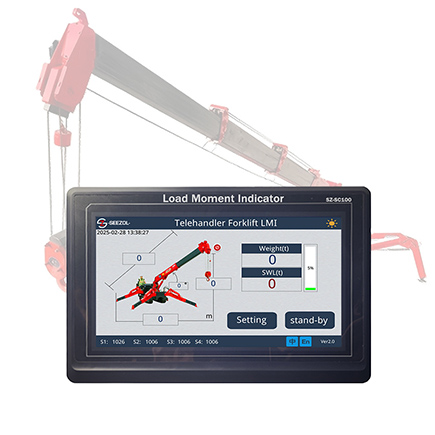
Monthly Maintenance
Performance Test: Use standard loads to simulate working conditions, check the alarm function and the accuracy of moment calculation, and calibrate and repair the system in a timely manner when the deviation exceeds the limit.
Data Recording and Analysis: Record the maintenance details and operation data in detail, analyze the trends of alarms and faults, and predict potential fault risks.
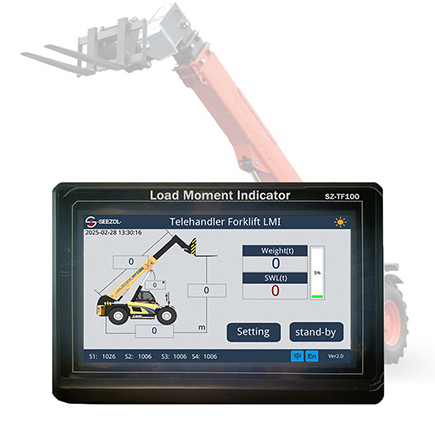
Annual Maintenance
In-depth Overhaul: Disassemble the system for a comprehensive inspection, clean the components, replace the worn parts, upgrade the software, test the hardware, and recalibrate the system.
Personnel Capacity Enhancement: Organize professional training for maintenance personnel, assess their maintenance skills, and optimize personnel management according to the assessment results.
Planning Formulation: Formulate the maintenance plan for the coming year based on the annual maintenance and the working conditions of the equipment, and prepare sufficient spare parts and maintenance tools.