The efficiency of wheel loader weighing systems directly impacts material transportation costs and operational economics, requiring comprehensive evaluation from three dimensions: time efficiency, measurement accuracy, and energy consumption.
1. Time Efficiency
Single Weighing Time: Traditional manual measurement takes 3-5 minutes per vehicle, while automated weighing systems require only 10-15 seconds, improving efficiency by over 12 times.
Continuous Operation Capability: Dynamic weighing technology enables seamless “loading-weighing-unloading” processes, achieving 85% equipment utilization (compared to ≤60% with traditional methods).
2. Impact of Measurement Accuracy
A 1% reduction in system error can decrease material waste by approximately 0.8 tons per shift.
With dynamic compensation algorithms, measurement stability improves by 40% under typical working conditions (RSD < 2.5%).
3. Energy Consumption Economics
Intelligent weighing systems reduce no-load energy consumption by 15%-20% through optimized hydraulic control logic.
Automated data upload functionality cuts manual recording time, lowering overall operating costs by 30%.
Bottleneck Analysis:
There is a trade-off between system response speed and hydraulic system inertia. The current optimal balance is:
When the sampling frequency ≥50Hz, the measurement accuracy-to-energy consumption ratio reaches Pareto optimality.
5G transmission latency (<20ms) already meets real-time requirements.
Future efficiency improvements will rely on deeper integration of edge computing and digital twin technologies.
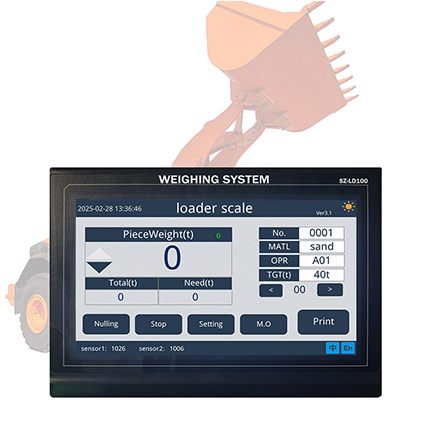