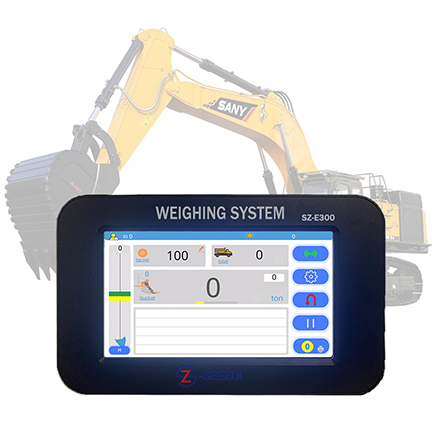
The impact of environmental factors on the accuracy of the excavator weighing system is mainly reflected in aspects such as temperature, vibration and shock, humidity and dust, and electromagnetic interference. The details are as follows:
Temperature
Changes in sensor performance: Temperature changes can cause the zero point and sensitivity of the weighing sensor to drift. Generally speaking, when the temperature rises, the metal material expands, and the size of the sensor’s elastic body changes, which in turn changes the internal stress distribution, resulting in deviations in the output signal. At low temperatures, changes in properties such as the hardness and elastic modulus of the material also reduce the measurement accuracy of the sensor. For example, when operating in a hot summer environment, the sensor may experience zero – point drift, causing the weighing result to be higher or lower than the actual value.
Impact on the hydraulic system: Temperature has a significant impact on the viscosity of hydraulic oil. High temperatures reduce the viscosity of hydraulic oil, increasing leakage in the hydraulic system and leading to unstable pressure. This affects the lifting and lowering speed and stability of the excavator bucket, resulting in inaccurate force transmission during weighing. Low temperatures increase the viscosity of hydraulic oil and the flow resistance, slowing down the response of the hydraulic system, which also has an adverse effect on weighing accuracy.
Vibration and shock
Interference with sensor signals: The vibration and shock generated during the operation of the excavator can cause fluctuations in the output signal of the weighing sensor. Different vibration frequencies and amplitudes have different impacts on the sensor. When the vibration frequency is close to the natural frequency of the sensor, resonance may occur, greatly increasing the measurement error. For example, during high – intensity impact operations such as rock crushing, strong vibration and shock can cause the sensor to output abnormal signals instantaneously, leading to inaccurate weighing data.
Loosening of the mechanical structure: Long – term vibration and shock may cause the mechanical connection parts of the weighing system to loosen, such as loose mounting bolts of the sensor and worn connectors. This changes the installation position of the sensor, leading to uneven stress and affecting the weighing accuracy.
Humidity and dust
Degradation of electrical performance: A high – humidity environment can cause the electrical components of the weighing system to get damp, reducing the insulation performance and easily leading to problems such as short – circuits and leakage, which affect the normal operation of the system. For example, when the humidity is high, the signal wire of the sensor may experience signal attenuation or interference due to moisture, resulting in fluctuations in the weighing data.
Wear of mechanical parts: After dust enters the weighing system, it may accumulate on the moving parts of the sensor and mechanical transmission parts, increasing friction and affecting the normal movement of the parts and force transmission. Dust may also block the filters and pipelines of the hydraulic system, leading to hydraulic system failures and indirectly affecting the weighing accuracy.
Electromagnetic interference
Interference with signal transmission: There may be various electromagnetic interference sources at the construction site, such as nearby high – voltage power lines, electric welders, and radio transmitting equipment. These electromagnetic interferences can interfere with the signal transmission lines of the weighing system through electromagnetic induction and electromagnetic radiation, drowning out the weak electrical signals output by the sensor and causing errors or fluctuations in the weighing data.
Malfunction of electronic components: Strong electromagnetic interference may cause malfunctions or logical errors in the electronic components of the weighing system, such as amplifiers and controllers. For example, electromagnetic interference may cause the controller to receive incorrect signals, resulting in incorrect processing and display of the weighing data.